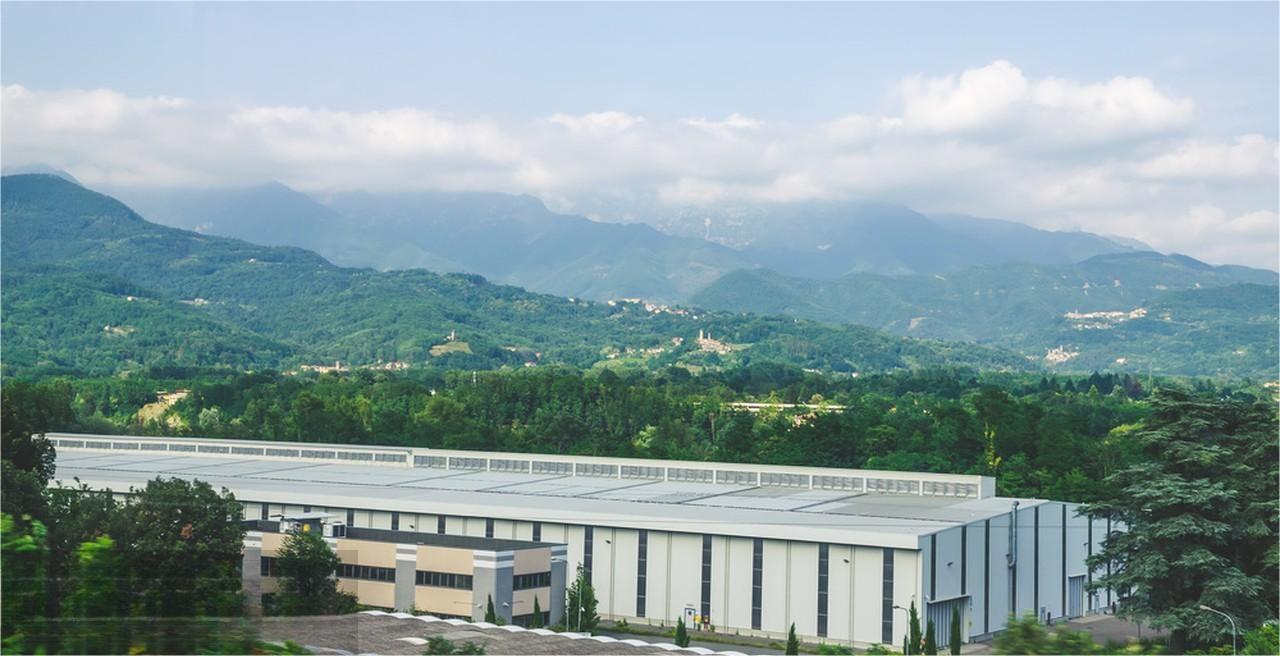
- Home
- >
News
A fluid reservoir for a pump mechanical seal is an essential component of the sealing system, particularly for double seal arrangements. It serves several important functions: Buffering: It provides a buffer for the process fluid, preventing it from coming into direct contact with the atmosphere, which can be critical in applications where the process fluid is hazardous or toxic. Pressure Control: The reservoir can help in maintaining a stable pressure within the seal chamber, which is crucial for the proper functioning of the mechanical seal. Lubrication: It can act as a source of lubrication for the seal faces, reducing friction and wear. Cooling: In some cases, the fluid reservoir can also serve to cool down the process fluid, preventing overheating of the seal faces. Flushing: It can provide a means for flushing the seal chamber with clean fluid, which is especially important in applications where the process fluid is abrasive or corrosive. Compensation for Thermal Expansion: The reservoir can compensate for any thermal expansion or contraction of the process fluid, maintaining the correct volume and pressure within the seal chamber.
HWGS gas seals typically consist of a stationary seal ring and a rotating seal ring. The seal faces of these rings are usually made of a hard material like silicon carbide or carbon graphite, which provides a smooth, wear-resistant surface. The seal faces are kept apart by a thin film of gas, which is supplied under pressure to the seal chamber. This gas film prevents direct contact between the seal faces, reducing friction and wear, and thereby extending the life of the seal.
selecting a hand refill pump for mechanical seals, it is important to consider the specific application requirements, including the type of fluid being handled, the operating conditions, and the necessary safety and reliability features to ensure the pump meets the needs of the system it will be used in.
The HWCS1 cyclone separator operates on the principle of centrifugal separation, separating solid particles from the pump discharge pipeline and transporting them to the mechanical seal chamber through the overflow outlet point of the cyclone. This type of equipment is crucial for preventing the leakage of hazardous liquids such as crude oil and sulfuric acid, while allowing the pump shaft to rotate relative to the static pump body. The design and understanding of the geometric parameters of a cyclone separator are crucial for ensuring the cooling flow rate and pressure drop of mechanical seals, in order to ensure effective cooling and operational integrity of the sealing surface
The Plan 53B system is a closed loop piping system that circulates and isolates liquids between sealed double seal arrangements to cool and lubricate the inner and outer seals. The system provides circulation through an internal pump ring and uses a heat exchanger to remove heat.
Cryogenic bellows seals are engineered to meet the demanding requirements of cryogenic service, especially Hanway HWZH-2 and HWZH-3,including high pressure, low temperatures, and the need for a tight seal to prevent leakage of the cryogenic fluid. They are rigorously tested for leak detection and often achieve extremely low leak rates, which is a testament to their reliability and tight-seal capacity