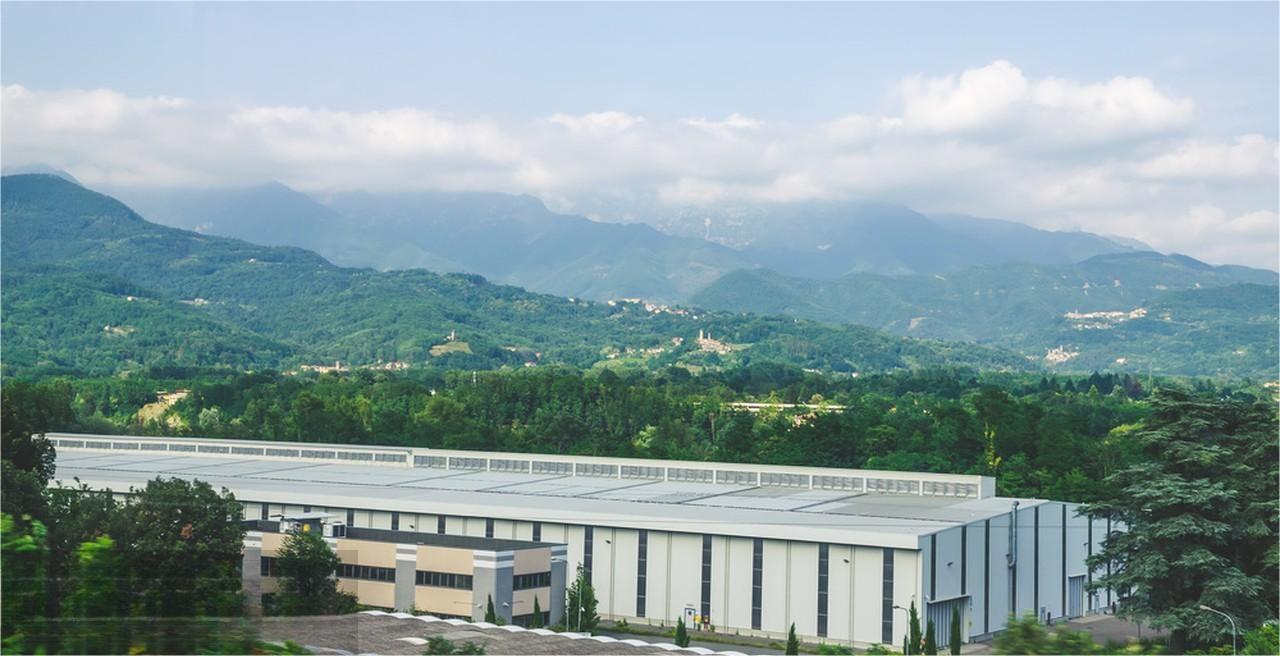
- Home
- >
- News
- >
- Product News
- >
News
we can supply various mechanical seals, such as metal bellows seal, cryogenic metal bellows seal, CrO coated stainless steel ring, wave spring and rubber ring, mechanical seal supporting system, fluid reservoir, hand refill pump, heat exchanger, cyclone dust separator, dry gas face, cartridge mechanical seal and long sleeve metal bellows seal, etc..
The function of this equipment is based on the principle of natural balance of adjacent adsorbent loads. In the drying stage, the adsorbent adsorbs water from the gas with high pressure flowing through the GZ-120/25 Molecular sieve high pressure acetylene gas dryer manual adsorber. During regeneration, a small amount of depressurized dry gas is replayed and regenerated through the adsorbent adsorbing water. Use the adsorption released by the gas in the drying process to heat the regeneration gas with reduced temperature after decompression, so as to improve the regeneration effect and reduce the regeneration consumption.
our small oxygen gas diaphragm compressor parameters for GD-85/35-300 are as below: inlet pressure 35bar, outlet pressure 300bar, flow 85Nm3/h and medium oxygen gas
small type Z diaphragm compressor is mainly used for laboratory, collecting various gases, and some of compressor are also installed in the container for compressing gases during movement.
Diaphragm compressors have multiple advantages, making them very popular in specific application fields. Here are some of the main advantages of diaphragm compressors: high gas purity, leakage prevention, quiet operation, low maintenance, high energy efficiency, high reliability and wear free compression.
acetylene gas is used with oxygen gas for cutting, in order to produce acetylene gas, our factory especially a set of simple production line to produce about98% purity acetylene gas to satify our customers' requirements
Corrosion resistance: The CrO coating provides an additional corrosion-resistant layer, which helps protect stainless steel materials from chemical corrosion, especially when used in harsh chemical environments. Wear resistance: The coating may enhance the wear resistance of the sealing ring, which helps to extend the service life of the mechanical seal and reduce the frequency of maintenance and replacement. Reduce friction coefficient: Coatings may help reduce friction between the sealing ring and the corresponding sealing surface, which can reduce energy loss and improve mechanical efficiency. Good sealing performance: The CrO coated sealing ring is designed to achieve a good sealing effect, preventing the leakage of liquids or gases, which is crucial in pumps, valves, and other rotating equipment. High temperature endurance: The coating may enhance the performance of the sealing ring under high-temperature working conditions, which is particularly important for mechanical seals used in high-temperature environments. Material compatibility: CrO coating may improve compatibility with different process fluids, enabling it to resist corrosion from various chemicals, including acids, bases, and solvents. Reduce maintenance: Coatings may reduce the maintenance requirements for sealing rings, as coatings can reduce wear and corrosion, thereby reducing the need for regular inspections and maintenance. Improving system reliability: By reducing leakage and enhancing sealing performance, CrO coated sealing rings help improve the reliability and safety of the entire system. Environmentally friendly: The use of CrO coating may reduce environmental risks caused by seal failure, as it reduces the leakage of chemicals into the environment.
Cyclone dust separator HWCS 2 "is a device used for cleaning aqueous liquids containing dirt and solid particles, and can transport the cleaned liquid to sealed areas or other required areas. The design features of this device include standardized design, optional housing materials, and threaded connections that meet most commonly used connection requirements
The heat exchanger of mechanical seals is an important component used to cool the mechanical seal barrier/buffer/flushing fluid, which helps to reduce the temperature of the sealing surface, thereby optimizing sealing performance and lifespan.
Low temperature bellows sealing is a sealing technology used in extreme low temperature environments, which ensures the safety of pumped fluids while providing long-term reliability. When designing pumps for transporting low-temperature fluids, special designs are often used, such as vertical multi-stage double shell pumps according to the American Petroleum Institute (API) 610 standard. These pumps have a heating chamber called a cofferdam that can thermally isolate the shaft seal from the cold pumped fluid, allowing for the use of traditional sealing techniques
The HW800 dry running bellows cartridge seal is suitable for the most common standards and extended sealing chambers of ANSI, DIN, and metric pumps. Its bellows inner diameter is designed with a 45 degree chamfer to ensure stress dissipation in each bellows plate and maximize its service life. It is suitable for pipeline sealing applications in fields such as petroleum, chemical, power, pharmaceuticals.
Famious Hanway industries' type HW606 is a high-temperature and corrosion-resistant rotating corrugated pipe component that uses different materials Including heat treated AM350 or Alloy 718 bellows, low expansion alloy sealing surface retainer, and 316 stainless steel wheel hub and housing and Inconel material. They can reliably seal fluids in harsh high-temperature corrosive environments and provide excellent sealing surface stability at high temperatures.